Im folgenden Kapitel soll eine Einführung in den Aufbau von Membranen und Modulen gegeben werden. Während in dieser Arbeit ein Schwerpunkt auf die Entwicklung neuer Materialien für Membrantrennschichten gelegt wird, zeigt diese Übersicht auf, dass für die Übertragung der Ergebnisse auf die technische Applikation weitergehende Arbeiten erforderlich sind.
Die wesentlichen Größen der Membrancharakterisierung – Permeabilität und Selektivität – werden definiert und der spezifische Energieverbrauch für die Trennung, auch in Bezug auf den Wirkungsgrad von Energiespeichersystemen, wird diskutiert.
Inhaltsverzeichnis
2.1 Aufbau von Membranen und Modulen
2.1.1 Membranmorphologie
Membranen können prinzipiell als poröse oder nicht poröse Schichten vorliegen. Die Transport- und Trennmechanismen in diesen Membrantypen unterscheiden sich grundsätzlich (vgl. Kap. 4.1). Poröse Schichten sind im allgemeinen um mehrere Größenordnungen permeabler für Gase als dichte Polymerfilme.
Bei den nicht porösen Membranen kann man wiederum homogene und asymmetrische Membranen unterscheiden. Da bei Membranen eine möglichst hohe Permeabilität pro Fläche erwünscht ist, müssen homogene Membranen möglichst dünn sein. Dies widerspricht jedoch der Forderung nach mechanischer Stabilität. Daher werden Membranen in der Regel als asymmetrische Membranen ausgeführt, bei denen sich eine sehr dünne, dichte Trennschicht auf einer porösen Unterstruktur hoher Permeabilität befindet. Besteht diese Trennschicht aus dem gleichem Polymer wie die poröse Stützschicht, spricht man von integral-asymmetrischen Membranen. Handelt es sich bei der Trennschicht um ein anderes Material, spricht man von Komposit-Membranen.
In Abbildung 2 ist der prinzipielle Aufbau einer Komposit-Membran gezeigt:
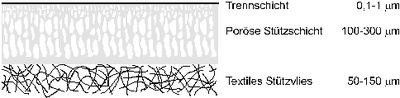
Auf ein textiles Stützvlies wird eine mikroporöse Schicht aufgebracht, welche die eigentliche Trennschicht unterstützt. Da kleine Defekte oder Poren in der Trennschicht bereits zu großen Verlusten in der Selektivität von Membranen führen, wird die eigentliche Trennschicht oftmals durch eine Schicht eines hochpermeablen Polymers (meist Polydimethylsiloxan, PDMS) bedeckt, was die Poren verschließt und zusätzlich die dünne Schicht mechanisch schützt [13, 14]. Diese Erfindung verhalf der Gastrennung mit Membranen zum technischen Durchbruch.
Bei Gastrennmembranen gibt es prinzipiell zwei geometrische Gestaltungsmöglichkeiten: Flachmembranen (vgl. Abbildung 2) und Hohlfasermembranen.
Bei Hohlfasern wird die Trennschicht innen und/oder außen auf die tragende, meist poröse Faser aufgebracht.
2.1.2 Membranmodule
Die Trennapparate, in die Membranen eingebaut werden, bezeichnet man als Membranmodule. Sie müssen die getrennte Führung von Feed- und Permeatstrom auf den beiden Membranseiten ermöglichen (Abbildung 3).
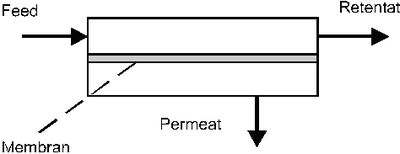
Das Gasgemisch, das dem Trennapparat zugeführt wird, wird als Feed bezeichnet. Im Trennapparat wird dieser Stoffstrom geteilt, als Permeat wird der Strom bezeichnet, der die Membran durchdringt, als Retentat der Teilstrom, der abgereichert die Trenneinheit verläßt. Für die Gasführung im Permeator sind verschiedene Strömungsvarianten möglich. Bei der in Abbildung 3 gezeigten handelt es sich um eine Kreuzstromführung. Wird der Permeatraum kontinuierlich mit einem Spülgas beaufschlagt, ist das entweder im Gegen- oder im Gleichstrom zur feedseitigen Strömungsführung möglich.
Flachmembranen können in Platten-, Taschen- oder Wickelmodule eingebaut werden. Ähnlich einer Filterpresse ist ein Plattenmodul (vgl. Abbildung 4) konstruiert [15]. Je ein Paar Membranpaar wird, durch einen Abstandhalter (Feedspacer) getrennt, mit der Trennschicht zueinander gestapelt. Zwischen jedem Paar wird als Abstandhalter ein Permeatspacer eingelegt. Die Spacer sind in Rahmen eingebettet, die gleichzeitig die Modulabdichtung und die Stoffführung durch alternierend angeordnete Kanäle und Bohrungen ermöglichen.
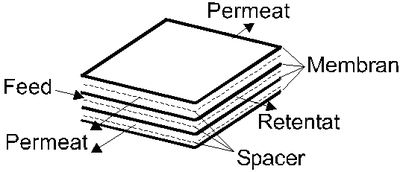
In Abbildung 5 ist der Aufbau eines Wickelmoduls [16] gezeigt:
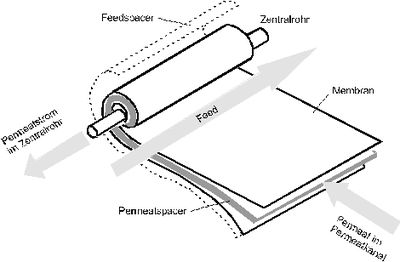
Eine Anordnungsmöglichkeit beim Wickelmodul ist, dass zwei Membranen mit der Stützschicht gegeneinander, getrennt durch den Permeatspacer, auf ein mit Bohrungen versehenes Rohr gewickelt werden. Die Membranrückseiten und der Permeatspacer werden dabei miteinander am Rand verklebt. Die gesamte Anordnung wird dann in ein Druckrohr eingebracht. Eine weitere Modulform für Flachmembranen ist ein Membrantaschenmodul [17], bei dem verschweißte Membrantaschen um ein mit Bohrungen versehenes Rohr zu einem Wickel angeordnet sind.
In Abbildung 6 ist ein Hohlfasermodul gezeigt. Hohlmembranen werden dazu bündelweise an den Enden in ein Kunstharz eingebettet. Permeatseitig sind die Hohlfasern offen, bei der hier abgebildeten Modulvariante ist ein Ende der Hohlfasern verschlossen.

Die vorgestellten Modulformen unterscheiden sich im wesentlichen durch die erreichbare Packungsdichte (Membranfläche pro Modulvolumen) und den Herstellungspreis, der bei Plattenmodulen relativ hoch ist im Vergleich zu Spiral- und Hohlfasermodulen (vgl. Tabelle 3).
Modultyp | Fläche pro Volumen m2·m-3 |
Platte | 400-600 |
Spiral | 800-1000 |
Hohlfaser | 2000-5000 |
Somit wird verständlich, warum technische Anwendungen nahezu ausschließlich mit Hohlfasermodulen (z.B. Membrankontaktoren [19]) ausgestattet werden. Für Labortests und Membranentwicklung wird jedoch wegen der leichteren Herstellbarkeit defektfreier Flachmembranen und der einfachen Modulform diese Ausführungsform gewählt (vgl. Kap. 5.2 ).
2.2 Kenngrößen von Gastrennmembranen
Die wichtigsten Kenngrößen von Gastrennmembranen sind deren Permeabilität und Trennfaktoren. Aus diesen Eigenschaften ergeben sich die Trennleistung und der Membranbedarf für eine Trennaufgabe.
2.2.1 Permeabilität
Durch ein Membranstück mit der Fläche A stellt sich bei stationären Bedingungen unter der Triebkraft einer Partialdruckdifferenz für ein Teilchen ein Fluß J (Einheit: kg·m-2·s-1) ein. Die Permeabilität P für ein permeierendes Gas einer Membran wird normiert als Gasvolumenstrom pro Membranfläche, Zeit und Partialdruckdifferenz angegeben (Einheit: Nm3(STP)·m-2·h-1·bar-1, STP: 0 °C, 101325 Pa, 22,414 l Molvolumen). Sollen Membranmaterialien miteinander verglichen werden, ist eine Normierung auf Membranfläche, Partialdruckdifferenz und Membrandicke üblich (Einheit: „barrer“ 10 -10·Ncm3(STP) cm·cm-2·s-1·cmHg-1, Umrechnungsfaktor zu obiger Einheit: P · Dicke Membran / cm · 2,0911 · 10 7).
Gewünscht sind Membranen mit möglichst hoher Permeabilität, da dies die notwendige Membranfläche für eine Trenneinheit verringert, weil eine membranabhängige minimale Dicke existiert, ab der erst defektfreie Membranen gefertigt werden können.
2.2.2 Trennfaktor
Die Trennleistung eines Membranmaterials wird mittels des Trennfaktors α angegeben.
Der Trennfaktor für ein Gaspaar A, B ist definiert als das Verhältnis der Gaspermeabilitäten P (vgl. Gl. 4). Der Trennfaktor ist eine von der Temperatur T, dem Feeddruck pF und der Druckdifferenz ΔpF-P über die Membran abhängige Materialkonstante. Als idealen Trennfaktor bezeichnet man das Verhältnis der Einzelgaspermeabilitäten (in dieser Arbeit verwendete Definition). Werden die Permeationsmessungen mit Gasgemischen durchgeführt und daraus die Permeabilitäten der einzelnen Gase bestimmt, spricht man vom realen Trennfaktor. Dieser ist nur mit dem idealen Trennfaktor identisch, wenn weder die Gase miteinander noch die Gase mit der Membranmatrix wechselwirken.
Der Trennfaktor α entspricht der Selektivität S für den Grenzfall, dass die Partialdrücke der Komponenten A und B im Permeatraum gegen 0 gehen (manchmal wird auch dieser Wert in der Literatur als idealer Trennfaktor bezeichnet). Die Selektivität S ist definiert als das Verhältnis der Stoffmengenanteile xF(A,B) im Feed und Permeat xP(A,B) für die Gase A (schneller permeierend) und B (vgl. Gl. 5) [20].
Die Bestimmung von Trennfaktoren wird meist bei niedrigen Drücken und niedrigen Druckdifferenzen durchgeführt (vgl. Kap. 6.1.1). Dadurch werden Quellungseffekte der Polymere, Komprimierung (hohe Drücke) und anisotropes Membranverhalten (hohe Differenzdrücke) reduziert. Zum Vergleich von Materialien, die sich nur geringfügig unterscheiden (z.B. variierte Substituenten in der Polymerseitenkette) ist es deshalb üblich, Permeabilitäten und Selektivitäten extrapoliert auf einen Feeddruck von 0 und auf eine Druckdifferenz von 0 anzugeben [vgl. 21, S. 24].
Trennfaktoren sind näherungsweise nicht von der Membrandicke abhängig. Ausnahmen sind Membranen mit sehr dünnen Trennschichten (< 0,1 μm) im Vergleich zu isotropen Filmen (100 μm). Fromm, Pinnau und Koros fanden Abweichungen von 10-20% bzgl. der Selektivitäten und führen diese u.a. auf die veränderte Polymermorphologie sehr dünner Schichten zurück [22]. Wie aus Gl. 5 ersichtlich ist, führt ein großer Wert für den Trennfaktor α zu großen Produktreinheiten (Verhältnis xP(A)/ xP(B)) der schneller permeierenden Komponente im Permeat.
Eine Berechnung der Zusammensetzung des Retentats ist über die Massebilanz des Moduls möglich (vgl. Kap. 6.1.3).
Ist Aufgrund von Reinheitsanforderungen an das Produkt eine mehrstufige Anlagenausführung (Verschaltungsmöglichkeiten [23A]) notwendig, macht sich ein niedriger Trennfaktor α der Membran insofern negativ bemerkbar, dass dann zurückzuführendes Permeat (z.B. bei einer Serienschaltung) wieder komprimiert werden muss und damit der spezifische Energieverbrauch des Verfahrens steigt. Der Trennfaktor α ist auch für die Produktausbeute neben der Partialdruckdifferenz die entscheidende Größe [23B]. Stellt z.B. das Retentat das Produkt der Trennanlage dar und soll das Permeat verworfen werden (vgl. Abbildung 1), so ist der Verlust über das Permeat um so geringer, je größer der Trennfaktor α ist.
2.3 Energieverbrauch der Gastrennung mit Membranen
Bei Prozessen der Energiespeicherung oder -gewinnung (vgl. Kapitel 1.3.1 ) kommt dem spezifischen Energieverbrauch der Gastrennung eine besondere Bedeutung zu, da dadurch der Gesamtwirkungsgrad eines solchen Prozesses wesentlich bestimmt wird und damit auch die Konkurrenzfähigkeit zu konventionellen Methoden.
Für die Berechnung des minimalen Energieverbrauchs für die Zerlegung einer Gasmischung mit den Komponenten A und B kann man von folgender Modellvorstellung ausgehen (vgl. [24], S. 92) : in einem Kolben befindet sich eine binäre Gasmischung mit den Stoffmengenanteilen xA und xB, die durch das Zusammenführen zweier Kolben getrennt wird. Die Kolben bestehen aus Membranen, die jeweils ideal selektiv für eine der Komponenten sind und dem Durchtritt der Komponenten keinen Widerstand entgegensetzen. Die für die Trennung aufzuwendende Arbeit entspricht der reversiblen Zerlegungsarbeit [25]. Für ein mol Gas beträgt die minimale isotherme Zerlegungsarbeit w min (vgl. Gl. 6):
Der Betrag ist gleich der freien Mischungsenthalpie ΔGm. Die isotherme Zerlegungarbeit w min ist maximal für äquimolare Mischungen und beträgt 1,7 kJ·mol -1 (0,0213 kWh·Nm-3 Mischung) bei 25 °C.
Die minimale Zerlegungsarbeit wird aber in jedem Falle überschritten, da keine ideal selektiven Membranen existieren und eine Membran einer permeierenden Komponente immer einen gewissen Widerstand entgegensetzt. Im realen Fall ist für die Gastrennung mit nicht porösen Membranen die Kompressionsenergie für den Feedstrom aufzubringen. Die für die adiabatische Kompression notwendige Arbeit ist in Gl. 7 angegeben [25].
Dabei ist η der Wirkungsgrad des Kompressors, γ das Verhältnis der Wärmekapazitäten cp/cv und q die Anzahl mol Gas, die pro Sekunde komprimiert wird. Durch das Entspannen des Retentats über eine Turbine kann jedoch Kompressionsenergie zurückgewonnen werden.
Für eine energetische Betrachtung des Prozesses sind noch der Energieverbrauch einer permeatseitig evtl. installierten Vakuumpumpe, Druckverluste im Modul und der Transportwiderstand über die Membran hinzuzurechnen. Mulder [25] gibt für das Beispiel einer Anlage zur Gewinnung von 35%igem Sauerstoff aus Luft (10 t·h-1) die in Tabelle 4 aufgelisteten Energieverbrauchswerte an.
Prozess | Produktreinheit 02/% | Energieverbrauch kWh |
Reversibel isotherm | 100 | 6,0 |
Kryogen | 99,5 | 62,7 |
PSA | 90 | 77,2 |
Membranen | 35 | 50,9 |
Die Werte aus obiger Tabelle zeigen, dass der tatsächliche Energieverbrauch in diesem Fall beim 8,5fachen des theoretischen Minimalwertes liegt.
Für ein Wasserstoffspeichersystem auf Basis von Ameisensäure (vgl. Abbildung 1) läßt sich analog folgendes berechnen: Die Verbrennungsenthalpie eines Normkubikmeters äquimolarer CO2/H2-Mischung beträgt 1,529 kWh. Nach Gl. 6 ergibt sich die minimale Zerlegungsarbeit zu 0,0213 kWh·Nm-3, das sind 0,0174 kWh pro kWh (η = 80%, Brennstoffzelle) elektrische Leistung. Mit den Vergleichswerten aus Tabelle 2 sind somit bei 25 °C ca. 14% der erzeugten elektrischen Energie für die Abtrennung von CO2 notwendig.
Beim mobilen Einsatz eines solchen Systems ist davon auszugehen, dass CO2 nicht zwischengespeichert, sondern an die Umwelt abgegeben wird. Für die Realisierung eines CO2-neutralen Prozesses (vgl. Kap. 1.2), muss CO2 für die Ameisensäureherstellung daher unter Wirkungsgradverlust einem Abgasstrom (z.B. Kohlekraftwerk, s.u.) entnommen werden. Geht man von einem durchschnittlichen CO2-Gehalt der Abgase von 13% aus [26], so berechnet sich mit Gl. 6 (Verbrennungsenthalpie Kohle 33 MJ·kg -1, η = 45%, 0,88 kg CO2 pro kWh elektrische Energie) die Zerlegungsarbeit bei 25 °C zu 957 kJ·mol-1 CO2, das entspricht pro kWh elektrischer Energie 0,0053 kWh Zerlegungsarbeit (200 °C 0,0084 kWh). Vergleicht man technisch übliche reale und minimale Zerlegungsarbeit (Tabelle 4), so ist zu erwarten, dass ca. 4% (bei 200 °C Abgastemperatur: 7%) der im Kraftwerk erzeugten elektrischen Energie für die Abtrennung von CO2 notwendig sind (PSA: 10-20% [27]).